- UseCase
- 製造
トヨタがアンドンの改善に着手、工場データが連携するIndustrial IoTの実現目指す
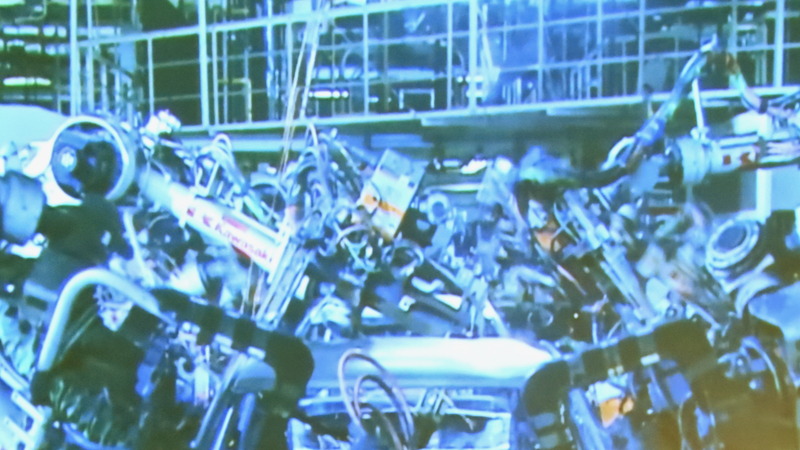
「トヨタ生産方式(TPS)」を生み出したトヨタ自動車の工場では、今も数々の“カイゼン”が続けられている。同社の溶接工程を担うMS車体生技部 ボデー技術統括室の担当者が、東京で2019年8月に開かれた「Industrial IoT Meeting」(主催リンクス)に登壇し、不具合への早期対応を可能にする“アンドン”システムにおける現場での改善状況について説明した。アンドンは、どのように進化するのだろうか。
トヨタ自動車は、車体を生産するボデー工場を海外26カ国と国内に持ち、それぞれで58ライン、18ラインを稼働させている。ボデーは、プレス、溶接、塗装、組み立てという工程で製造される。その中で溶接を担当するのが、MS車体生技部ボデー技術統括室である(写真1)。
同社Mid-size Vehicle CompanyのMS車体生技部 ボデー技術統括室 汎用技術開発グループ長の林 哲史 氏は、「自動車業界は今、100年に1度の大変革期にあるとされ、生き残っていくためには『早く』『安く』『高品質』な車を顧客に届けることが使命になる」と強調する(写真2)。
ただ溶接工程においては、「連続稼働と品質を維持するために、機能別にシステムを構築し、後工程に迷惑をかけないように“自工程完結”を目指してきた。だが、工程で発生した不具合の原因を追究するための情報が不足しているほか、システム間連携も困難な部分最適な状態になっていた」と打ち明ける。
不具合対応の早期化するための“アンドン”のシステムにおいても、「約20年利用しており老朽化していた。システム構成自体が古く、データ連携が難しくなっていた」(林氏)という。
気づき与えるアンドンも結果の表示だけでは限界に
アンドンは、工程の異常を関係者に通知するための仕組みである。「異常/停止」なら赤色の、「消耗品交換指示、品質確認指示」なら黄色の、「消耗品交換中、品質確認中」は白色のランプが点灯し、生産台数や稼働率、停止時間など生産性の低下につながる工程を知らせる。トヨタにとって「現場でカイゼンが必要な点について気付きを得るためのツール」(林氏)である。
1 つの工場にアンドンは十数画面が表示されている。工場全体の状態を表示する「総合アンドン」と、製造ラインの詳細を表示する「サブアンドン」がある。異常が発生すれば、総合アンドン、サブアンドンとたどって異常工程を探すこともある。
ただ林氏は「現状のアンドンは、結果を示す情報からアクションを起こすしかない。現場に駆けつけても処置のためのツールが足りずに手戻りが発生することもあれば、異常対応の順番が不明確なため復旧計画を立案するだけの情報も足りなかった。加えて固定表示のため、情報が増えてくると見づらくなり、単純に情報量を増やすことにも限界がある」と課題を説明する。
そもそも自動化の進展で、製造用ロボットは800台近くが稼働し、工程を制御するPLC(Programmable Logic Controller)も150~200台が設置されている。「情報収集の設定と収集後の整理の負荷が大きく、システム更改の構想はあっても、これまで手が出せなかった」(林氏)のが実状だ。
結果、「日報は手書きのままで、自動では収集できなかった。報告書フォーマットも統一できず、工場ごとの独自運用になっていた」と林氏は説明する。