- Column
- IoTのラストワンマイルを担うLPWAの基礎知識
LPWA との親和性が高いFA(ファクトリーオートメーション)【第2回】
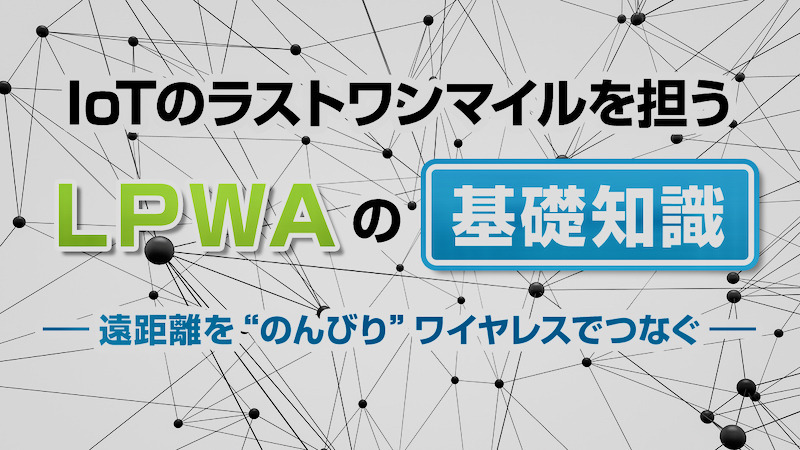
前回、IoT(Internet of Things:モノのインターネット)“ラストワンマイル”を支える通信網としての「LPWA(Low Power Wide Area)」について紹介した。今回は、LPWAの適用業務のなかでも、特に親和性が高いFA(ファクトリーオートメーション)について紹介する。両者の親和性の高さは、お客様や業界関係者との会話から肌で感じているところである。
工場内がセンサーの山であることは今も昔も変わらない。筆者がPLC(Programmable Logic Controller)やセンサーを売り歩いていた20年以上前ですら、工場に入れば生産ラインや空調機器など、ありとあらゆるところにセンサーが満ちあふれていた。光学センサーや近接センサー、安全センサー、空圧センサー、温調器、油圧センサー、流量センサーなどなどである。
しかし、どれだけセンサーがあってもデータの可視化が、なかなか進まない。予算が潤沢な大企業なら工場全体をシステム化し集中管理を実施しているが、日本の屋台骨を支えるのは、やはり中小企業。彼らの工場では大規模な管理システムを導入できず、センサーに表示される数値を現場で目視確認し、メモ帳に記録していた。それが今でもまかり通っている。
センサーの巡回点検をなくせば工場の資産価値が高まる
工場の広さを400メートル×100メートルとすれば、センサーが異常値を指していないかを点検するために工場を1周すれば1キロメートル以上歩く計算になる。24時間で3回点検なら3キロメートルだ。体力的にもきついが、この人手不足の時代に、センサーの点検に毎日1時間を浪費するのは、どう見ても無駄である。
工場中に点在するセンサーデータを「できれば日々のメンテナンス費用程度の低い予算で」「大した工事もなく」「難しいプログラムなどなしで」手元で見える化できるのがLPWA(Low Power Wide Area)ネットワークだ。手元ですべてのセンサーデータが見られれば、先述の長距離を歩かなくて済む以外に、工場の生産技術者にはどのような変化が起こるだろうか。
修理のプロである生産技術者といえども、そもそも機器類には壊れないでほしいと願っている。センサーデータを見える化できれば、故障を予知し壊れそうなところをリストアップして予知保全が可能になる。
予知保全では故障率が下がり楽になるだけではなく、故障によってラインを止めずに済むため、工場全体のタクト(生産率)向上に直結する。打算的に話せば、同じ工場でも単位時間当たり生産数量が増えるわけだから、工場そのものの資産価値が高まることになる。
工場の資産価値としての値上がり金額は、LPWA機器を購入し現場に設置する金額と比べると、数ケタ単位で大きくなることは容易に想像できるだろう。かたやLPWAの電波を発する電子機器、かたや工場全体の資産価値の数%である。
では、どんなデータを見れば予知保全が可能になるのだろうか。その例を列挙する。
例1:負圧で製品を吸着し別の位置に搬送する真空ピックアップ
小さな、もしくは軽い製品を作っている工場でよく見られるのが、この真空ピックアップのゴム製のパットが劣化し、ひびや割れが生じている姿である。こうした劣化が出てくると従来、たとえばマイナス50キロPa(パスカル)の真空圧を出せたものが最大でもマイナス30キロPaしか出せなくなる。ひびや割れから空気が漏れているからだ。
もちろん、まだ交換しなくても動いてはいるのだが、いずれ製品をピックアップできずにどこかに放り投げた細かなパーツが不良を巻き起こす。もしくは「パッド交換」アラームが突然出てラインが止まるという事態に見舞われる。そんな時に限って交換パッドの在庫がなかったりするのである。
真空ピックアップのアームには一般に負圧の圧力センサーがついている。そのセンサーのアナログ出力(4〜20ミリアンペアや1〜5ボルト)を無線で飛ばせれば、理屈上、生産技術者の手元のタブレットで状態を把握でき、目視では難しい“多少の劣化状態”でパッドの交換、すなわち予知保全が可能になる。