- Column
- “稼ぐ力”に向けた中小企業の共創とデジタル技術の使い方
山口製作所、プレス加工にこだわり金型の内製化から冷間鍛造を活用した工法転換を拡大【効率化編】
自作の社内システムで受注から生産計画までを自動化
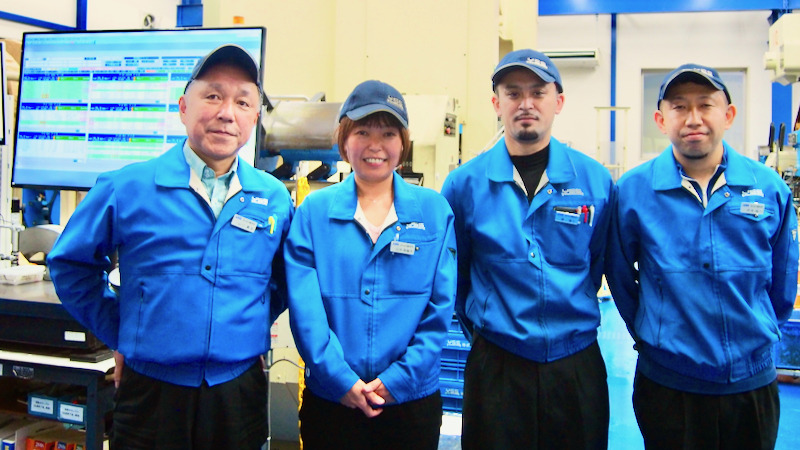
山口製作所(新潟県小千谷市)はプレス加工と金型製造を主力にする、従業員数28人の中小製造業である。1968年に創業し、2000年からは金型の内製化にも取り組んできた。最近は、自社開発した金型と、デジタルを含めた測定などにより、一般には切削やダイキャストで製作する部品をプレス加工で製作し、従来とは異なる市場への参入を実現している。【効率化編】では、同社が進めてきた社内システムの自社開発によるペーパレス化や業務の自動化への取り組みを紹介する。
新潟県小千谷市にある山口製作所は、従業員数28人のプレス加工会社である。手がけている製品の多くは「手のひらサイズ」と呼ばれる大きさの部品だ。現社長の山口 貴史 社長の父親が1968年に創業した。だが大学を卒業する年に他界されたため、1987年に当時23歳で代表に就任した。
当時の山口製作所は、自宅を使った典型的な町工場で「製品1個1円」といった加工賃が収益源だった。プレス加工のための金型は100%外注しており、顧客から受注があれば、顧客の費用で金型を製造し、プレス部品を製造していた。結果「技術的な付加価値や納期など全く自社でコントロールできなかった」と山口社長は振り返る。
その後、金型の内製化に取り組み、2000年に放電加工のためのワイヤーカッター1台を導入。約2年間の試行錯誤を経て金型を自社で製造できるようになった。そこから「顧客から受け取った図面通りに製造するだけでなく、自分たちが意図する“ものづくり”ができるようになり、利益率も高まってきた」(山口社長)という。
プレス加工の技術力も高まった。たとえば、一般には切削加工の手法で製造するミリ波レーダー用の部品をプレス加工で製造することで、「70%のコストダウンを実現した」(山口社長)。顧客に工法転換を提案するなどで、従来とは異なる市場にも参入している。現在の顧客数は約30社で、月に750~1000件の案件をこなす。
間接作業は全くのムダ、極力なくしたい
プレス加工の取り組みに触れる前に、山口製作所の生産管理など社内システムの徹底度合いを紹介したい。同社では、受注から出荷までの一連の業務プロセスにおいて、キーボードによるデータの手入力を、ほぼ全廃できているからだ。そこまで徹底する理由を山口社長は、こう説明する。
「製造に伴う間接作業は全くムダであり、極力なくしたい。最新の加工機を導入すれば加工作業の効率化が進むが、間接作業の効率化を図るほうが会社に与える効果は大きいはずだ。最近は、難しい仕事が増え、そうした状況に対応するためにも業務の効率化は不可欠である。属人的な部分をなくし、設計技術と職人技、組み付け/取り付け調整といった作業以外は、すべて数字で評価し、だれでもできるようにしたい」
同社を「数字を重視する会社」にしている背景には、山口社長が比較的に若い時に社長に就いたことがある。「技術的経験が何もなく、顧客に納得してもらうためには、数字で結果を提示すしかなかったため」(山口社長)だ。
山口製作所の効率化に向けた取り組みは歴史が長い。1980年代には、まだ珍しかったPCを導入し伝票管理を開始。1990年代から受注管理や在庫管理、生産管理の自社開発に取り組んできた。2000年代に入るとペーパレス化を推進。各種ドキュメントや帳票をデジタル化し、サーバー上で管理するようにした。
この間に、無線LANなども導入し、社内環境も整えている。2020年1月時点では、社内ネットワークには約120台の機器がつながるなど、業務遂行に不可欠な道具になっている。文書管理システムも「ISO(国際標準化機能)などの認証取得する際には、対応が容易になるなど役だった」と山口社長は話す。
同社の業務システムは基本、自社での独自開発だ。初めて開発したのは、納品書作成システムである。製品情報をマスター登録しておき、製品情報や部品番号、製品名、単価などを自動で記載する。当時は自動車関係の仕事が多く、「受注に先行して、さまざまな伝票を作成しなくてはならず、それらを手書きで発行するのが大変だった」(山口社長)からだ。
受注データから作業計画を自動で作成
そこから開発対象を広げ、現在は受注から出荷までをキーボードレスで進められる仕組みを実現している。その中核にあるのが、受注・生産管理システムだ。同システムでは、受注状況をリアルタイムに把握でき、部品や製品、材料の在庫を確認しながら、どの加工機では、どの製品を、いくつ作らなければならないかの作業計画までを自動で計算する(写真1)。材料などの発注書も自動で作成できる。
従来、生産計画は製造部門が表計算ソフトのExcelを使って個別に立てていた。材料発注も手作業のため、そこがボトルネックにもなっていた。現行システムでは計画が自動で作成できるため「生産計画の作成に関わっている人員はゼロ」(山口社長)である。