- Column
- “稼ぐ力”に向けた中小企業の共創とデジタル技術の使い方
山口製作所、プレス加工にこだわり金型の内製化から冷間鍛造を活用した工法転換を拡大【高付加価値化編】
プレス加工の精度をデジタル化し品質を可視化
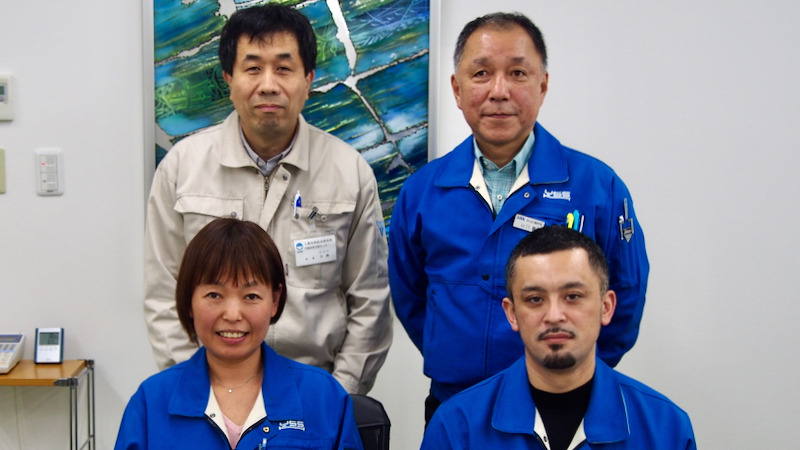
山口製作所(新潟県小千谷市)はプレス加工と金型製造を主力にする製造業である。【効率化編】では、同社が1980年代から進めてきた社内システムの自社開発によるペーパーレス化や業務の自動化への取り組みを紹介した。【高付加価値化編】では、一般には切削やダイキャストで作る部品をプレス加工で製造するなど、同社の“ものづくり”現場での取り組みを紹介する。
山口製作所は、プレス加工により、主には「手のひらサイズ」の大きさの部品を製造している。2002年からは金型も自社で製造することで、「自分たちが意図する“ものづくり”ができるようになり、利益率も高まってきた」と山口 貴史 社長は胸を張る。
サポイン事業採択を契機に研究機関との連携が常態に
プレス加工の技術力向上には継続して取り組んでいる。大きな転換になったのは、2012年に経済産業省が実施する「戦略的基盤技術高度化支援事業(サポイン事業)」に採択されたことだ。テーマは「リチウムイオン電池用タブリードの高精度せん断加工技術の開発」である。
タブリードは、リチウムイオン電池に取り付ける電極のこと。純アルミや純銅の焼きなまし材といった柔らかな材料を使うため、高精度・高品質なタブリードを安価に量産するのが難しい。これをサポイン事業では、独自の金型などの新技術を開発し、せん断加工によって製造できるようにした。
同事業では、新潟県工業技術総合研究所や新潟大学などと連携し研究開発に取り組んだ。山口製作所が研究機関の元を訪れたのは、これが初めてだった。山口社長は、「サポイン事業への申請は当初、敷居の高い制度だと感じていた。研究機関との連携に対しても、新潟県工業技術総合研究所などへは製品検証などのためにたびたび訪れていたものの、共同研究などはおこがましいという感覚があった」と当時を振り返る。
それが最初の採択後は、毎年のように共同研究などに取り組んでいる。新潟県などからの支援も受けながら、県内の長岡技術大学や、プレス加工研究で著名な日本工業大学などと積極的に連携している。これらの人脈の多くは「過去に参画したサポイン事業でのつながり」(山口社長)という。
プレス加工技術の向上により、たとえば、ダイカスト(鍛造)手法で作るのが一般的だった部品を、プレス加工で製造することを可能にし、「ミリ波レーダーの部品では70%のコストダウンに成功した」(山口社長)。現在は、工法の転換を含めた提案を顧客にし、これまでとは異なる市場に出て行っている。
山口社長は「従来、切削加工でなければできなかった部品をプレス加工でも製造できる新しい工法が開発できれば、顧客にも当社にもメリットがある。新工法の開発には今後もチャレンジしていく考えだ」と強調する。
2019年度も「高性能モータ用アモルファス箔積層モータコアのプレスせん断加工量産技術の開発」というテーマでサポイン事業に採択されている。今後3年の予定で新潟県工業技術総合研究所や日本工業大学らと共同研究を進める予定だ。
技術開発に向けては、プレス荷重データの解析にも取り組んでいる。解析結果を基に、プレス以外の加工法で製造していた製品を、プレスで加工できないかを検討するためだ。そのためにプレス加工機にセンサーなどを設置している。現状では「ある程度の荷重データしか可視化できないことが解ってきている。もう一歩踏み込んで加工法などを工夫できるだけの仕組みを検討している」(山口社長)という。
ロボットを導入し、さらなるムダ取りに挑戦中
新潟県工業技術総合研究所との共同研究では、ロボットの導入にもつながっている。まずは検査工程にロボットを導入し、現場作業員を3人から1人に削減できた。これもサポイン事業からのつながりによるものだ。当初は、ロボットベンダーの製品を検討していたが、新潟県工業技術総合研究所の大野 宏 氏から、オープンソースソフトウェアの「OpenCV」を提案され、同ソフトウェアを使った仕組みを構築した。
検査ロボを土台に現在は、加工後の部品をロボットでピッキングする仕組みを開発中だ(写真4)。プレス加工後の部品をディープラーニング(深層学習)で画像認識し、ロボットでピッキングすることで後工程の自動化を狙う。
ただ山口製作所が製造する部品は「小さい、薄い、中が抜けている」など、画像認識の面でも、ロボットハンドでつかみ上げるという面でも扱いが難しい形状のものがほとんど。ロボットメーカの担当者からも「現状の画像認識では無理だと言われた」(山口社長)くらいである。そんな部品のピッキングが実現できれば、「後工程が劇的に変わるはず。間接業務の自動化にさらに拍車がかかる」と山口社長は強調する。